Questo articolo è stato pubblicato da ASCCA News – house organ di ASCCA – Associazione per lo Studio e il Controllo della Contaminazione Ambientale
Gli HPAPI (Highly Potent Active Pharmaceutical Ingredients) costituiscono un segmento in rapida espansione nell’industria farmaceutica globale. Attualmente, oltre 1.000 small molecules altamente potenti sono in fase di sviluppo, e le stime di mercato prevedono una crescita annua di circa il 10% in questo settore. Alla fine del 2022, oltre il 40% di tutti i farmaci in fase di sviluppo rientravano nella categoria di elevata attività. Un impulso ulteriore allo sviluppo del mercato è stato dato in tempi più recenti da HPAPI nella forma dei cosiddetti ADCs (Antibody-Drug Conjugates). La gestione dei HPAPI nel manufacturing farmaceutico richiede soluzioni appropriate per garantire la sicurezza e la salute dei lavoratori, oltre che per supporto al controllo della contaminazione e alla sostenibilità della produzione. In questo articolo si illustra l’approccio integrato del Containment Mix (CM), delineandone i contenuti per sommi capi e illustrando alcuni vantaggi tramite esempi applicativi che, come si potrà vedere, riconducono risultati e considerazioni agli elementi enunciati nel paradigma stesso.
Introduzione
In generale un HPAPI può essere definito in base a parametri di attività farmacologica, come ad esempio una dose terapeutica giornaliera pari o inferiore a 10 mg, a un limite di esposizione occupazionale (OEL) pari o inferiore a 10 μg/m3 TWA, a caratteristiche di alta selettività e/o potenzialità di causare cancro, mutazioni, difetti nello sviluppo o tossicità riproduttiva. Oppure ancora per la natura innovativa di un composto la cui potenza e tossicità non sono ancora completamente conosciute. Alla fine degli anni ’80 un gruppo di aziende farmaceutiche avviò un processo di definizione delle categorie di pericolosità per i principi attivi farmaceutici. Nel corso delle decadi successive, questo sistema è stato ulteriormente sviluppato, delineando in modo più completo tali categorie, oggi comunemente note come Occupational Exposure Bands (OEB). Non esiste uno standard armonizzato riconosciuto a livello internazionale per questa categorizzazione: solitamente essa comprende da 4 a 6 categorie ciascuna di un ordine di magnitudo, dove le sostanze meno potenti vengono assegnate alla prima categoria, mentre quelle più potenti vengono collocate in quella più elevata. Un esempio di tali categorie è riportato nella Figura 1.
Nel caso ci si trovi di fronte a una sostanza per la quale non sia possibile stabilire un OEL con i dati disponibili, quest’ultima può essere inserita in una delle categorie di potency e gestita secondo i controlli che essa prevede. È importante sottolineare che questa classificazione può essere adattata in base alle sostanze che si intendono produrre, alla strategia e ai risultati delle misurazioni, come quelli ottenuti con un Programma Strategico di Controllo del Contenimento (PSCC) di cui parleremo più avanti.
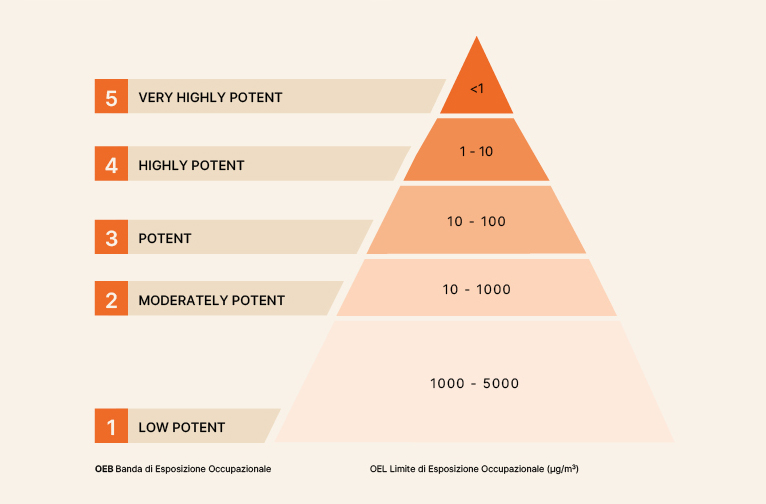
Figura 1 – Esempio di classificazione delle categorie di esposizione occupazionale
Vedremo inoltre come l’approccio al contenimento di sostanze o agenti chimici (e in particolare di HPAPI prodotti sia in bulk che processati in apposite formulazioni, oggetto di questo articolo) viene presentato come il contributo di una serie di elementi (il Containment Mix) di cui il PSCC è parte e al tempo stesso la driving force per il contrasto, il controllo e la limitazione della diffusione di queste sostanze nell’ambiente di produzione e, più estesamente, nell’ambiente interno ed esterno alla facility.
Metodologia
La domanda da porsi quando si parla di contenimento di principi attivi ad alta potenza, in tutte le fasi della produzione industriale e di laboratorio, non dovrebbe essere se esso sia necessario, ma piuttosto quale grado di contenimento sia richiesto per ciascun contesto. Tale approccio favorisce infatti lo spostamento dell’attenzione dall’uso delle tecnologie tout court a seconda del contesto contingente, di difficile giustificazione a utenti e autorit. regolatorie, all’adozione di strategie integrate che siano coerenti con l’approccio strategico e la cultura aziendale. L’adozione crescente, inoltre, di approcci di control banding all’interno dell’industria chimica e farmaceutica, con la definizione di percorsi specifici per la gestione delle sostanze in base al loro livello di pericolosit., suggerisce ulteriormente l’importanza di indagare le strategie di contenimento per tutti i principi attivi e in tutti i processi, siano essi legati alla produzione, ricerca, controllo qualit., logistica o manutenzione.
Nel presente articolo si introduce la forma del Containment Mix (CM) come paradigma di un approccio comprensivo, delineandone i contenuti per sommi capi e illustrando alcuni vantaggi tramite esempi applicativi che, come si potr. vedere, riconducono risultati e considerazioni agli elementi enunciati nel paradigma stesso.
Il CM pone l’accento sull’interdisciplinarit. delle competenze e delle funzioni dell’azienda, dimostrando come esse possano contribuire a raggiungere un obiettivo superiore rispetto a un approccio che non integra cos. ampiamente i vari aspetti. Una schematizzazione di tale approccio. riportata in Figura 2.
Gli elementi costitutivi del CM sono:
• Valutazione e sviluppo del processo
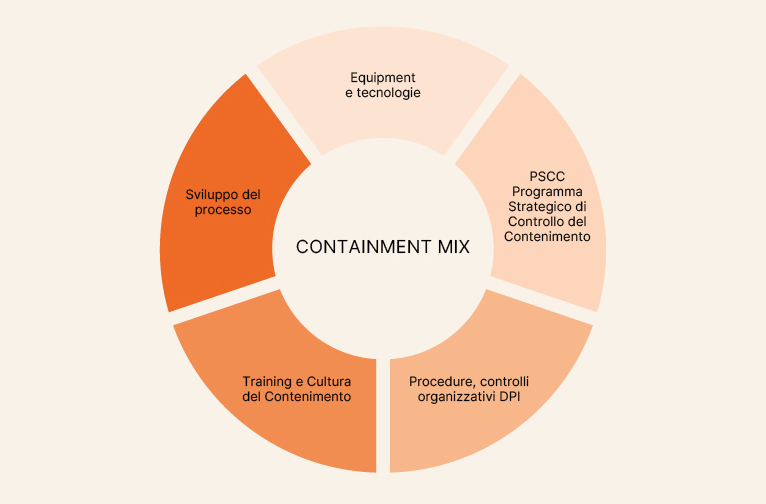
Figura 2 – Gli elementi del Containment Mix
• Training e cultura del Contenimento
• PSCC – Programma Strategico di Controllo del Contenimento
• Procedure, Controlli organizzativi e DPI
• Equipment e tecnologie
Ciascuno di essi, come è stato dimostrato da un ampio insieme di misurazioni in casi reali, ha un contributo significativo e determinante nel controllo dell’esposizione. L’applicazione degli elementi del CM richiede una guida che monitori continuamente l’evolu-zione di banding, proprietà delle sostanze, equipment, procedu-re e formazione durante l’intero ciclo di vita del processo. Come illustrato più avanti, questo può essere attuato tramite il PSCC.
Valutazione e Sviluppo del Processo
Durante lo sviluppo del processo vengono svolte attività essenziali per identificare, mitigare ed eventualmente eliminare i rischi legati alle sostanze presenti al suo interno, selezionando i reagenti appropriati e la loro combinazione, acquisendo dati sul rischio chimico e i limiti (OEL), nonché approfondendo il design del processo per gestire questi rischi in modo efficace. Esistono molti approcci risk-based per raffinare i processi durante la fase di sviluppo al fine di ridurre il rischio di esposizione, ed è fondamentale che la loro fattibilità venga analizzata fin dalle fasi iniziali. Il risultato di questo assessment potrebbe portare ad esempio a eliminare o sostituire solventi altamente tossici, a utilizzare reagenti o intermedi in sospensione in certe fasi di carico o trasporto, a ottimizzare il flusso del processo assicurando che i trasferimenti tra equipment di contenimento siano ridotti al minimo. In casi specifici, i tecnici potrebbero essere in grado di ridurre il numero di passaggi di sintesi, eliminando cos. intermedi isolati e il rischio di esposizione ad essi associato.
Equipment e tecnologie
In letteratura è ampiamente documentato l’uso di controlli ingegneristici ed equipment per il raggiungimento di obbiettivi di contenimento. Essi sono noti anche come misure di protezione collettiva poiché tutelano tutti i presenti nell’area di lavoro, a differenza dei dispositivi di protezione individuale (DPI) che proteggono individualmente chi li indossa. I sistemi di contenimento primario si riferiscono a quei controlli ingegneristici che limitano la diffusione di una sostanza fin dalla sorgente di contaminazione, solitamente interna agli equipment stessi. Il contenimento secondario, invece, si riferisce alle misure che limitano la diffusione della sostanza nell’area di produzione che può essere sfuggita al contenimento primario. Tra gli esempi di misure di contenimento primario troviamo isolatori utilizzati per la manipolazione di HPAPI, continuous liner e altre interfacce, macchine per la produzione di dosi solide orali (OSD), sistemi di trasferimento. Esempi di misure di contenimento secondario includono invece cleanroom, airlocks e gradienti di pressione tra esterno ed interno all’area di produzione. L’approccio più tutelante in termini di sicurezza dell’operatore, ma come vedremo con risvolti interessanti anche per contaminazione e sostenibilità, rimane il contenimento “alla fonte”, prediligendo i sistemi primari e regolando opportunamente in base a questi la scelta di quelli secondari. Vi sono due aspetti piuttosto comuni, emersi da anni di pratica professionale, che . bene evitare quando si parla di equipment: il primo riguarda la tendenza a basare l’intera strategia di contenimento esclusivamente sulla loro introduzione, trascurando l’importanza degli altri elementi del CM. In secondo luogo, sovente si vede come non venga riconosciuta la necessit. di testare gli equipment con una procedura rappresentativa delle reali operazioni che verranno condotte al loro interno, affidandosi a test non accurati e a procedure “generiche” che generano dati non corretti, spesso fuorvianti.
Training e Cultura del Contenimento
Una cultura del contenimento “consapevole del rischio” . elemento cruciale per il successo del programma. Diventa essenziale che i membri dell’organizzazione, a tutti i livelli, comprendano chiaramente ruoli e responsabilit. per garantire un Contenimento sicuro degli HPAPI. Il management dovrebbe dimostrare un forte impegno e guidare l’implementazione del programma, assicurandosi che siano allocate le risorse necessarie per i sistemi di contenimento, dalla progettazione alla manutenzione programmata e al mantenimento continuativo del PSCC. Gli operatori dovrebbero sentirsi responsabili non solo per sé stessi, ma anche per i propri colleghi, garantendo il corretto utilizzo dei sistemi di contenimento; dovrebbero essere inoltre incoraggiati a identificare e implementare continuamente miglioramenti a questi sistemi, discutendone direttamente con la dirigenza.
I dati raccolti in anni di assessment e testing hanno dimostrato che la perizia e l’esperienza del personale possono incrementare notevolmente i livelli di contenimento di un equipment; un programma efficace di formazione sulla sicurezza nella produzione di HPAPI pertanto dovrebbe essere adottato e reso obbligatorio con una certa frequenza per tutti gli operatori, lo staff che gestisce il programma di Controllo del Contenimento e altri soggetti che, a vario titolo, interagiscono con dette sostanze. Il piano di formazione continua dovrebbe sempre includere argomenti di carattere generale sui principi del contenimento e dell’igiene occupazionale, mirando principalmente a far comprendere la natura dei rischi associati all’uso di composti potenti in tutte le fasi dell’operativit., dalle operazioni routinarie alla manutenzione, dal cleaning ai failures fino alle emergenze. Poich. un controllo visivo non . sufficiente a rilevare situazioni di esposizione inaccettabile, (i livelli di sicurezza sono solitamente ben al di sotto della soglia visibile), un training efficace dovrebbe approfondire anche le caratteristiche di queste sostanze, spiegando cosa accade a questi livelli di pericolosit. in termini di possibili vie di emissione e diffusione, evidenziando cos. l’importanza di pratiche corrette e misure di contenimento anche complesse. Infine, per quanto riguarda gli equipment, una formazione adeguata dovrebbe includere non solo una puntuale verifica delle modalit. di utilizzo delle macchine, dei tools e delle interfacce, ma anche un’analisi approfondita dei punti critici delle principali tecnologie di contenimento presenti. In tempi recenti sono stati sviluppati tools virtuali in realt. aumentata che rendono molto efficace la fruizione di un training mirato all’utilizzo di un dispositivo piuttosto che la simulazione di un particolare task operativo o di gestione dell’emergenza.
Programma Strategico di Controllo del Contenimento
Come già introdotto il CM possiede al suo interno un elemento fondamentale, il Programma Strategico di Controllo del Contenimento (PSCC). Una sorta di regia delle strategie, delle valutazioni, delle misure, dei risultati e delle azioni di controllo necessarie per garantire che l’obiettivo di contenimento sia costantemente raggiunto e mantenuto nel tempo. È consigliabile formalizzare il PSCC in un programma strutturato, con linee guida definite, condotto da un gruppo di lavoro con competenze
diversificate, come igiene occupazionale, tossicologia, risk assessment, chimica analitica, qualità e ambiente. Questo team potrebbe includere sia figure interne all’azienda che esperti esterni. Il PSCC adotta un approccio risk-based al contenimento che affronta l’intero ciclo di vita di processi, come mostrato in Figura 3.
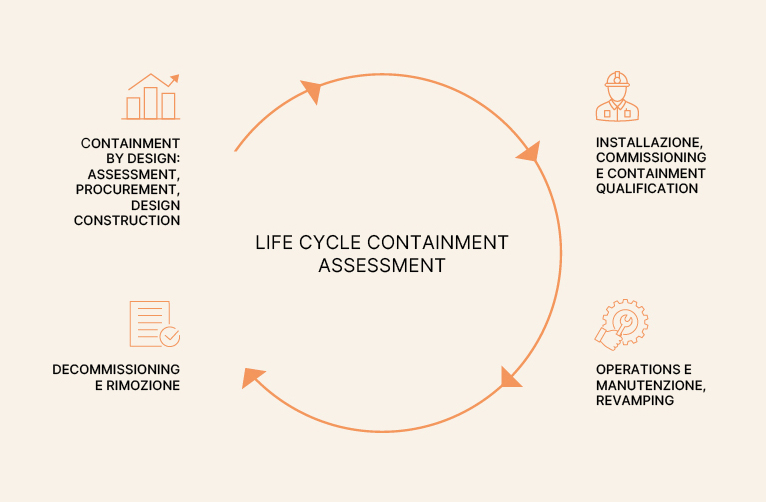
Figura 3 – Il Containment Life Cycle
Il focus del programma dovrebbe essere il più ampio possibile e includere sostanze, processi, equipment e dispositivi di protezione, OEL, OEB e rischi di esposizione, procedure e strumenti di monitoraggio, valutati secondo robusti riferimenti di settore e in linea con la strategia di control banding in uso. L’attività dovrebbe coprire progressivamente la nuova concezione o la rivalutazione periodica di tutti i processi di produzione, ricerca, controllo qualità, logistica e manutenzione, considerando tutte le attività routinarie e non routinarie, sia produttive che non produttive.
Il ciclo di valutazione del contenimento per nuove realizzazioni o revamping, ad esempio, condotto secondo questa modalità possiede fin dall’inizio una base fondamentale per il design, facilitando anche il procurement tecnico e la definizione delle richieste per i fornitori di tecnologie. Nella fase successiva di commissioning e qualifica, sarà fondamentale ottenere la prova delle effettive performance attraverso dati misurati e campioni raccolti durante monitoraggi standardizzati e riproducibili, (come quelli descritti nelle metodiche SMEPAC di ISPE).
Considerata l’importanza di confrontare i risultati nel tempo e comparare diverse tecnologie, reparti e stabilimenti distanti tra loro, il concetto di riproducibilità qui assume un valore ancora maggiore, rendendo imprescindibile l’utilizzo di metodi di test standardizzati e condotti all’interno di un programma capace di darne un’adeguata valutazione. La fase di operatività dei processi che ne segue può avere una durata variabile, da giorni ad anni, a seconda della tipologia dei dispositivi utilizzati (ad esempio, le glove box flessibili sono solitamente impiegate per periodi brevi) e della vita produttiva del principio attivo, molto diversa ad esempio tra ricerca e sviluppo, formulazione per fasi cliniche e produzioni su larga scala. Anche in questa fase, il test di contenimento (SMEPAC), eseguito con una certa frequenza in base alle risorse disponibili, alla strategia adottata e ai risultati pregressi, è fondamentale per confermare tramite misurazioni reali il mantenimento del controllo di equipment, procedure e dispositivi di protezione. Combinando la frequenza di questi test con un robusto piano di monitoraggio dell’igiene industriale, focalizzato sull’esposizione a principi attivi nelle attività considerate rilevanti nel risk assessment, si ottiene infine il massimo controllo possibile sulla contaminazione e sulla conseguente potenziale esposizione. Nella fase finale di dismissione degli equipment l’attenzione si concentra sulle modalità operative per lo smontaggio o lo smantellamento dei sistemi, che devono essere oggetto di valutazione e, se necessario, di miglioramenti di tipo procedurale o tecnologico. Un caso di particolare interesse a causa della sua elevata criticità e frequenza in questa fase è la dismissione di sistemi single use di contenimento (dai dati raccolti questi task sono solitamente a rischio di esposizione maggiore rispetto alla stessa operatività).
Di seguito sono riportati alcuni tools utili allo sviluppo e mantenimento del PSCC:
• Determinazione di PDE (esposizione massima giornaliera accettabile) e di OEL;
• Determinazione di limiti accettabili di contaminazione superficiale (ASL);
• Sviluppo di metodi analitici e di campionamento per determinazione di HPAPI nell’aeriforme, sulle superfici e in altre matrici;
• Risk assessment qualitativi/semiquantitiativi in diversi format con focus sul rischio di esposizione, criticità degli equipment, processi, ambiente ecc.;
• Containment test quantitativi con surrogato (SMEPAC);
• Campagne di monitoraggio di igiene occupazionale;
• Metodi di inattivazione e/o decontaminazione per API.
Esempi Applicativi
Riportiamo ora alcuni esempi tratti dall’attività di consulenza scientifica e testing svolte in diverse realtà di ricerca e produzione HPAPI, per comprendere perché è utile applicare questo approccio.
Attività di Ricerca e Sviluppo e Controllo Qualità
Un primo esempio è l’assessment e il testing di attività di laboratorio, condotta negli ultimi anni in alcuni reparti di Ricerca e Sviluppo e controllo qualità di facilities esistenti. Qui il risk assessment ha evidenziato i principali determinanti di esposizione e contaminazione identificando le tipologie di equipment, le quantità e lo stato fisico delle sostanze attive, la severità delle operations e le modalità operative. Alcune criticità tipiche di queste attività portate alla luce sono state ad esempio il dover valutare new chemical entities (NCE), i processi multistep non sempre standardizzati, l’utilizzo di equipment non sempre progettati per il contenimento e la minor segregazione delle aree rispetto alla produzione. In questo scenario alcuni componenti del CM quali training, modalità operative e containment culture, hanno rivestito un ruolo chiave. I risultati hanno portato a una caratterizzazione statisticamente adeguata delle apparecchiature e delle operazioni unitarie secondo le control bands in uso per attività di laboratorio, consentendo per la maggior parte la gestione di sostanze nelle fasce OEB3 e OEB4. I dati hanno inoltre permesso di identificare performance ancora migliori nei casi in cui lo stato fisico della sostanza attiva (liquido ad esempio) o la severità dell’operazione rappresentavano un “best case”, oppure, al contrario, di orientare le scelte verso la segregazione parziale o totale delle attività (sostanze in stato fisico solido o con severità e potency maggiore). Nei casi in cui i laboratori possedevano un’unità separata per la gestione di altamente attivi si è riusciti a definire con precisione l’ambito di applicabilità di queste aree in termini di OEB/OEL e a mantenerne sotto controllo il contenimento, revisionando nel tempo le modalità operative a seconda dell’evoluzione delle attività. Dal punto di vista del lifecycle containment, infine, i dati hanno permesso di evidenziare alcune differenze tra i sistemi moderni e quelli obsoleti e di pianificare monitoraggi pluriennali organizzati in base alla priorità delle situazioni più critiche.
Attività di produzione con isolatori flessibili
Il secondo esempio riguarda l’utilizzo in produzione di isolatori flessibili per operazioni in contenimento come dispensing, formulazione di lotti clinici e preparazioni di HPAPI per filling sterile. Questi sistemi realizzati in materiale polimerico trasparente e conduttivo sono utilizzati in massima parte per sostanze fino alla categoria OEB4, a seconda che siano passivi o mantenuti internamente a pressione negativa. Le tecnologie monouso offrono vantaggi in termini di costi e flessibilità di applicazione, adattandosi facilmente a impianti e strutture esistenti per migliorare in modo mirato i processi. In contesti multiprodotto inoltre, dove è richiesto un rapido turnover tra i prodotti, l’approccio monouso riduce o, idealmente, elimina la necessità di verifiche della pulizia. In varie esperienze condotte su sistemi flessibili la valutazione è stata applicata fin dalle fasi iniziali del progetto (containment design) per offrire un’adeguata performance di contenimento in tutti gli utilizzi previsti, proseguendo con un’approfondita considerazione del ciclo di vita dell’equipment. Il lifecycle di questa tipologia di sistemi di contenimento, infatti, è molto più breve dei loro analoghi fissi, e le operazioni di cleaning e dismissione diventano quasi routinarie in termini di frequenza. Dai risultati di misurazione è stato evidenziato che molti sistemi erano dipendenti dalle abilità e comportamenti dell’operatore e che alcune fasi di utilizzo, soprattutto non produttive come cleaning, collapsing e distacco degli stessi dalle strutture a cui erano stati integrati, mostravano criticità anche notevoli in termini di contenimento. Il programma ha permesso in molti casi l’allineamento degli elementi del CM alle caratteristiche specifiche di questa tecnologia. Ciò ha migliorato e mantenuto sotto controllo vari aspetti peculiari dell’operare con tali sistemi, come la necessità di formazione frequente, le operazioni complesse e talvolta non completamente definite a priori, i cicli di vita significativamente più brevi e le operazioni di dismissione eseguite con una frequenza quasi routinaria.
Attività di produzione in isolatori per altissimo contenimento
L’ultimo esempio descrive un’attività di sintesi HPAPI su scala del chilogrammo in suite dedicate servite da sistemi di complessità e performance di contenimento molto elevata (OEB5, range 0,01-0,001 μg/m3). Il contenimento secondario consiste in un’area segregata con accessi separati monodirezionali per materiali e personale, mentre il processo e il contenimento primario sono stati sviluppati in parallelo, realizzando un sistema «all in one» che integra in un unico equipment tutti gli step di reazione. Le attività infatti vengono svolte interamente sotto alto contenimento in una serie di camere di lavoro interconnesse e servite da passbox con interfacce CLS (Continuous Liner System) multiple. Questa configurazione elimina a monte la problematica del trasferimento tra diversi isolatori di processo e la conseguente potenziale contaminazione che ne potrebbe derivare. Al tempo stesso consente di utilizzare il sistema in modo modulare servendosi di parti e interfacce in/out e indipendente. Il CIP/ WIP è stato integrato nel design dell’equipment, minimizzando la necessità di estrazione di parti all’esterno e consentendo il ripristino del cleaning della macchina e delle apparecchiature interne quasi interamente in contenimento. La prima fase ha previsto un’analisi approfondita di tutte le operazioni unitarie degli step di sintesi che possono essere eseguiti con il sistema, nonché una verifica delle modalità operative di reparto, comprese le attività interne ed esterne al sistema isolato fino al limite dei corridoi. L’analisi ha incluso operazioni sia routinarie che non, sia produttive che non produttive, scomponendole fino ai task rilevanti per il contenimento. Successivamente è stato identificato per quali attività era prioritaria una valutazione quantitativa del contenimento e della conseguente potenziale esposizione, da attuare utilizzando i tools illustrati nella metodologia. La valutazione quantitativa è operata da anni continuativamente seguendo un piano pluriennale e utilizzando una combinazione di test di contenimento con surrogato e monitoraggi di igiene industriale. L’attenzione dei test di contenimento è rivolta principalmente alle potenziali emissioni provenienti dai sistemi di contenimento primario e secondario, mentre i monitoraggi si concentrano sulle possibili esposizioni degli operatori. Entrambi gli approcci hanno richiesto una fase preparatoria significativa, volta da un lato ad adeguare le modalità di campionamento ed analisi al grado di contenimento da testare e dall’altro a validare metodi di determinazione dell’attivo capaci di raggiungere i limiti di verifica richiesti. Nel corso degli anni il programma ha mantenuto il controllo continuativo del contenimento sulla base delle misurazioni acquisite, portando ottimizzazioni nelle modalità operative, nell’uso delle interfacce, nei metodi di analisi, nei punti di indagine e nei dispositivi di protezione aggiuntivi rispetto al contenimento primario.
Conclusioni
La produzione e formulazione degli HPAPI è un settore in sviluppo continuo che pone sfide significative per la sicurezza e la salute dei lavoratori e rende necessario un approccio avanzato al contenimento. È fondamentale comprendere che un programma di contenimento efficace non si limita ai controlli ingegneristici ma integra questi con elementi culturali, organizzativi e procedurali del Containment Mix (CM) durante l’intero ciclo di vita. Ciò garantisce efficienza, flessibilità e adattamento nei processi produttivi, massimizzando il successo degli investimenti e limitando soluzioni sovradimensionate (over-engineering). Questo approccio è particolarmente utile anche per riconsiderare più compiutamente le produzioni convenzionali, ad esempio sintesi di API o di forme farmaceutiche solide orali progettate originariamente quando l’indice di pericolosità delle sostanze era di ordine di grandezza inferiore. Il programma strategico di Controllo del Contenimento fonda le sue basi sull’ approccio risk-based e sulla verifica in campo grazie a misure confrontabili, ripetibili, raccolte dove necessario e con la miglior accuratezza possibile. I dati dei Containment test SMEPAC e delle misurazioni di igiene industriale, collezionati nell’ambito di un programma affidabile e monitorato nel tempo, sono fondamentali per la sicurezza dei dipendenti e possono fornire un contributo alla valutazione del rischio di contaminazione incrociata con altri prodotti. In termini di sostenibilità, l’assessment operato in modo integrato può contribuire al miglior bilanciamento tra tecnologie di contenimento primario e ventilazione secondaria, all’ottimizzazione delle necessità di DPI e dei processi di cleaning. Questo, come si è visto anche negli esempi applicativi, può portare ad un risparmio di risorse, energetiche, materiali o idriche. La riduzione dell’uso di DPI e l’ottimizzazione dei processi di pulizia, inoltre, se guidata da dati strutturati e consapevoli, consente anche di ridurre l’impatto ambientale, sia per quanto riguarda la generazione di rifiuti da inviare alla termovalorizzazione, sia per la quantità di principio attivo immesso dagli effluenti liquidi e gassosi dell’impianto. In definitiva la sviluppo di HPAPI parte dal presupposto di minimizzare le quantità di farmaco per ottenere il medesimo risultato a livello terapeutico, sviluppando sostanze che per loro stessa natura necessitano di un programma strategico di Controllo del Contenimento. Questo tipo di controllo è una condizione che, in generale, dovrebbe essere sempre ricercata e applicata non solo ai sistemi ad alto contenimento o ai principi attivi estremamente potenti. Il suo impatto positivo, infatti, può essere ampio, e coprire aspetti di processo, di protezione dell’operatore, di supporto a una strategia di controllo della contaminazione ed infine di contrasto alla diffusione delle sostanze chimiche nelle matrici ambientali.
Highly Potent Active Pharmaceutical Ingredients (HPAPIs) are a rapidly expanding segment of the global pharmaceutical industry. Currently, over 1,000 small molecules highly powerful are under development, and market estimates predict annual growth of approximately 10% in this sector. By the end of 2022, more than 40% of all drugs in development were re-entry in the high activity category. A further impetus to the development of the market has been given in more recent times by HPAPI in the form of the so-called ADCs (Antibody-Drug Conjugates). The management of HPAPIs in pharmaceutical manufacturing requires appropriate solutions to ensure the safety and health of workers, as well as to support contamination control and production sustainability. This article illustrates the integrated approach of the containment mix (CM), outlining its contents briefly and illustrating some advantages through application examples which, as can be seen, link results and considerations to the elements set out in the paradigm itself.
Questo articolo è stato pubblicato da ASCCA News – house organ di ASCCA – Associazione per lo Studio e il Controllo della Contaminazione Ambientale
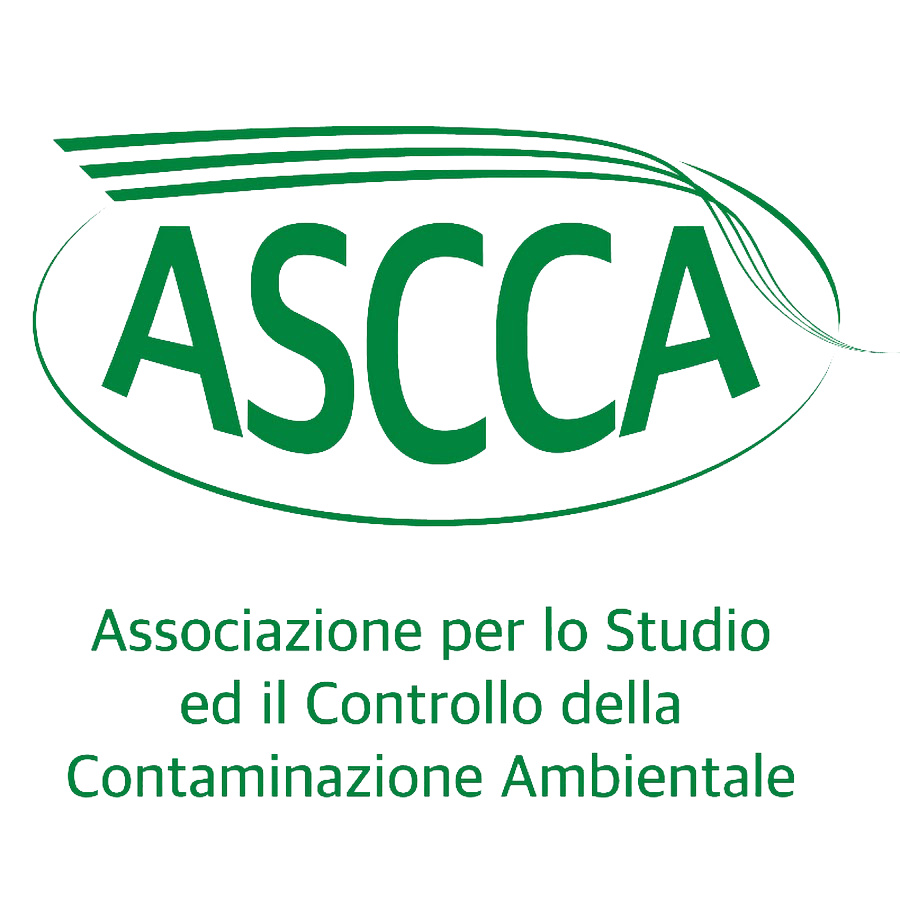
Articoli correlati
Luglio 31, 2025
BIM, VR e AR nella progettazione farmaceutica: efficienza, controllo e qualità integrata
Nel settore farmaceutico, la progettazione impiantistica è una sfida ad alta…
Luglio 17, 2025
Progettare con la simulazione fluidodinamica (CFD)
Da più di un decennio oramai Techniconsult integra la simulazione…
Febbraio 27, 2025
L’evoluzione della guida SMEPAC
Questo articolo è stato pubblicato da ASCCA News. Una nuova edizione della…