In the pharmaceutical industry, adoption of contamination control strategies (CCS) and the implementation of adequate quality risk management measures (QRM) are critical for organizations to guarantee product quality and safety. Computational fluid dynamics (CFD) simulation has emerged as a powerful tool to provide invaluable insights into fluid flow, heat transfer, contamination dispersion and control within the manufacturing environment.
Today, alongside GMP compliance, optimizing energy consumption and reducing the carbon footprint have become significant concerns due to the substantial ventilation airflows required for clean spaces and classified environments. By leveraging CFD simulation in HVAC design, pharmaceutical organizations can support contamination control strategies (CCS) as well as implement robust quality risk management practices, ultimately ensuring the production of safe and effective pharmaceutical products while driving sustainability initiatives.
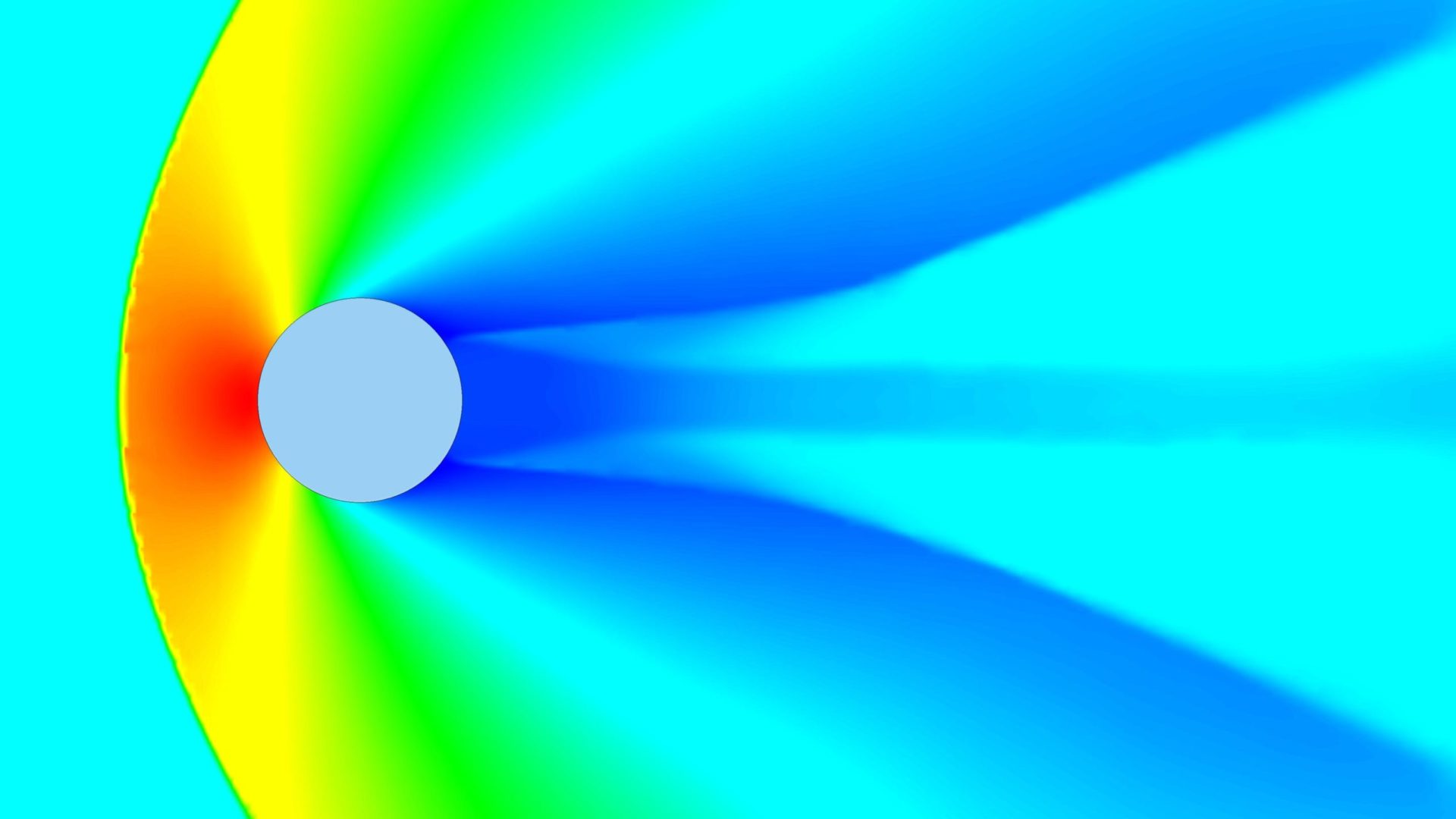
How CFD simulation can support Contamination Control Strategy (CCS) and Quality Risk Management (QRM)
Controlling contamination is of paramount importance in pharmaceutical plants to ensure product quality, safety, and compliance with regulatory standards. CFD simulation plays a pivotal role in supporting CCS and QRM by providing a comprehensive understanding of airflow patterns, particle dispersion, and the expected performance of cleanrooms. Through accurate modeling, CFD simulation helps identify potential contamination sources, evaluate the effectiveness of ventilation systems, and assess the system’s capability to respond to possible contamination events. By visualizing airflow patterns and particle trajectories, areas with inadequate performance can be identified, leading to the implementation of targeted mitigation strategies to minimize contamination risks. Moreover, CFD simulation aids in optimizing air filtration systems, cleanroom layouts, and operational procedures to enhance overall contamination control measures.
How CFD simulation can support sustainability initiatives
Computational Fluid Dynamics (CFD) simulation offers significant advantages in optimizing airflow design and associated energy consumption in classified areas within pharmaceutical plants. By accurately modeling and analyzing the airflow, CFD allows for the reduction of energy-intensive processes while ensuring operational efficiency, thus contributing to sustainability efforts.
Reducing Energy Consumption in Classified Areas at the design condition:
CFD simulation enables the optimization of design airflow rates in classified areas, leading to substantial reductions in energy consumption associated with ventilation systems. By fine-tuning the design airflow rates, pharmaceutical plants can ensure that the necessary cleanroom conditions are maintained while minimizing unnecessary energy expenditure; this results in cost savings and reduced environmental impact.
Supporting programs for Energy Savings in non-operational periods:
Thanks to simulation process, CFD can assist in the implementation of energy-saving programs by evaluating and reducing airflow rates during non-operational and unmanned periods. In unmanned conditions, HVAC systems for classified areas can maintain required performance levels with reduced airflow rates. CFD simulation aids in anticipating the performances of HVAC systems at reduced airflow conditions, identifying areas with inadequate performance, and enabling corrective actions early at the design phase.
Reduction of ventilation energy burden:
The energy consumption for ventilation is proportional to the cube of the supplied air volume. Consequently, even limited reductions in airflow rates can lead to a substantial decrease in energy consumption for ventilation systems. Reducing ventilation contributes to economic savings but also positively impacts the overall energy consumption of utilities production systems.
Enhancing Sustainability through CFD:
By leveraging CFD simulation, pharmaceutical companies can proactively pursue sustainability goals. Optimizing airflow rates and implementing energy-saving programs aligns with environmental commitments and reduces the plant’s carbon footprint. Additionally, reduced energy consumption contributes to overall sustainability by conserving natural resources and decreasing greenhouse gas emissions.
Figure N.1 – Example
Use of CFD for the optimisation of airflow patterns in a “grade B” filling room. Case description
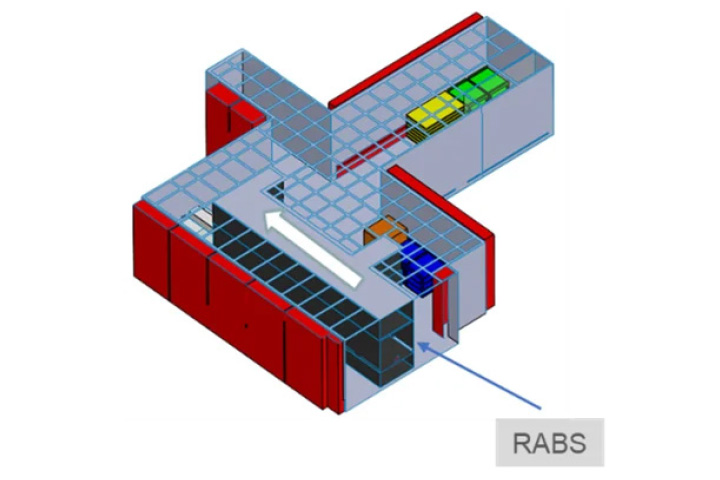
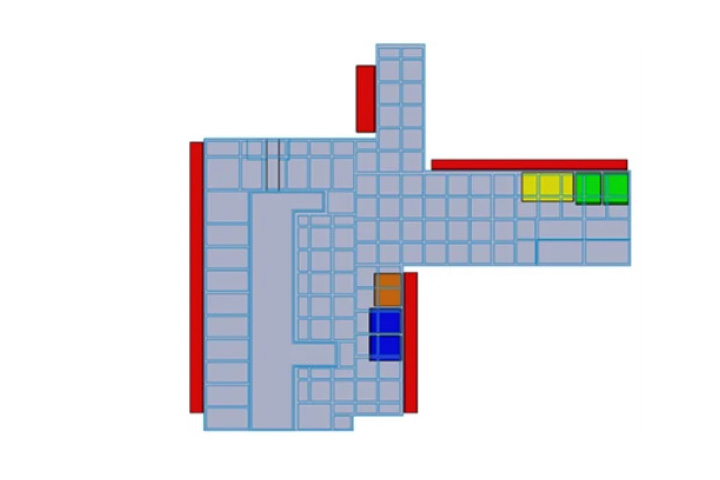
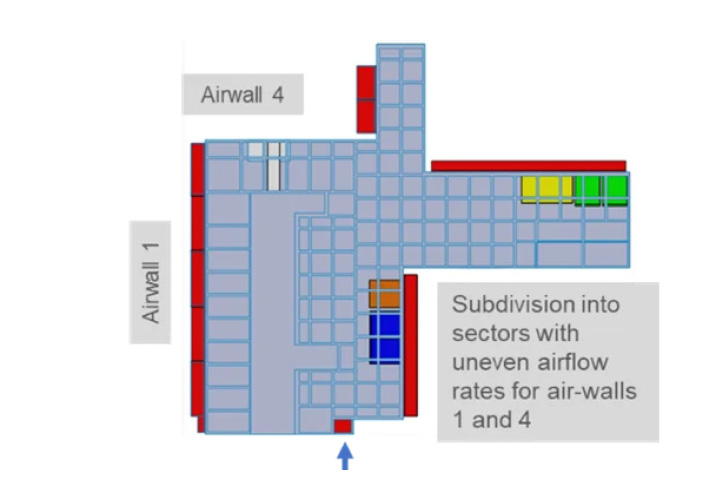
Problem: high quantity of air coming from the RABS and the HEPA ceiling to be returned to the HVAC system -> preliminary CFD analysis of airflow patterns inside the room -> difficulty to balance the system, risk of eddies.
Solution: Corrective actions and optimization of flows via the introduction of an additional air-wall and the sectorizing of two air-walls -> virtual balancing of the return airflow rates.
Results of CFD simulation
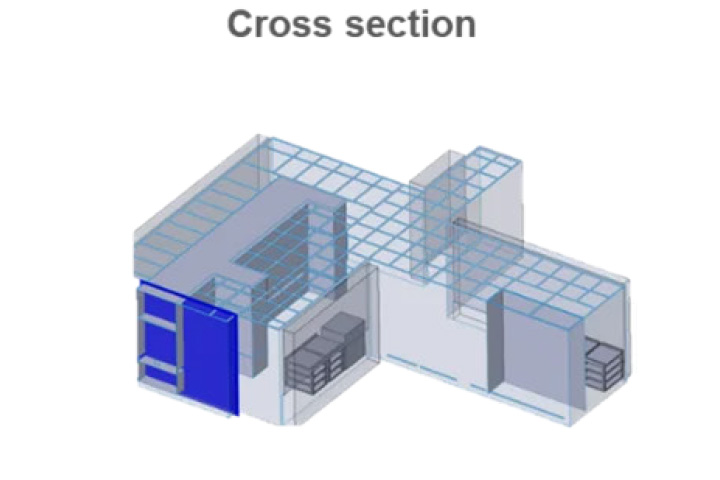
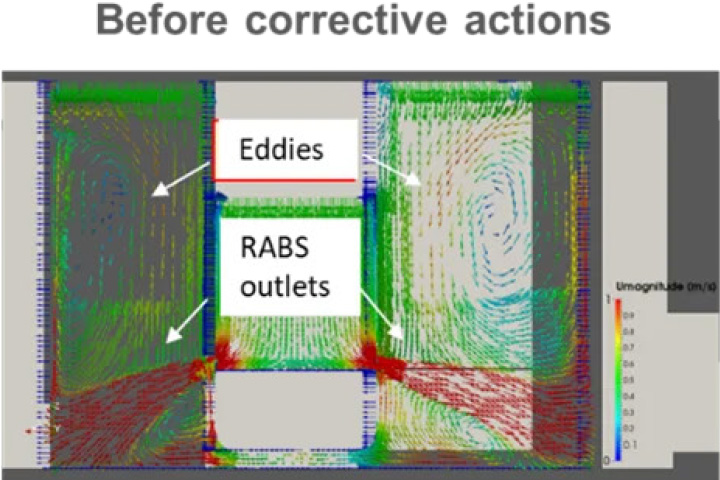
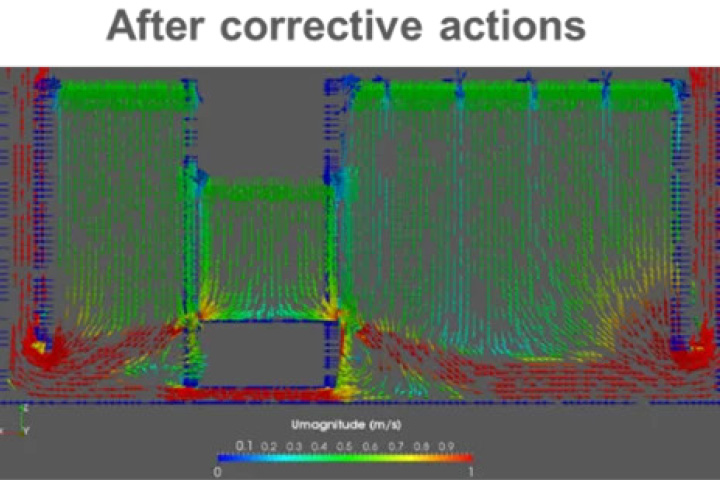
In general: airflow patterns after corrective actions are more even. Eddies shown in the section are eliminated and unidirectionality of air flow is much more present in the room space -> risk of back flow from floor level to critical areas (staging areas, open RABS outlets and mouse-hole) is reduced.
At the same time, this aerodynamic correction can support the reduction of room airflow rate during at rest conditions
Conclusion
CFD simulation has emerged as a powerful tool to support contamination control strategies, quality risk management, and sustainability initiatives in pharmaceutical plants. By accurately predicting fluid flow, heat transfer and contamination dispersion, CFD simulation enables organizations to make informed decisions, optimize processes, and ensure the production of safe and effective pharmaceutical products.
Articoli correlati
July 29, 2025
BIM, VR and AR in Pharmaceutical Design: Efficiency, Control and Integrated Quality
In the pharmaceutical sector, plant design is a highly complex challenge. Even…
July 17, 2025
Designing with Computational Fluid Dynamics (CFD)
For over ten years, Techniconsult has been incorporating Computational Fluid…
February 13, 2025
AI and BIM design: a new era for architecture and engineering
One of the most promising innovations is the integration of Artificial…